Need to design a cleanroom? With an increasing emphasis on maximizing product yield, improving quality control and ensuring safety, more companies than ever are looking to install cleanrooms and controlled environments in their facilities. This article is designed to answer the commonly asked question, "How do I design a cleanroom?"
Our Qualifications -
40 Years of Cleanroom Design Expertise
Our cleanroom design and construction experience extends over three decades and range from basic environmentally-controlled areas in manufacturing facilities to ultra-clean nano-technology labs and negative pressure isolation rooms to help control infectious disease.
The following article presents a brief overview of how cleanrooms are classified, as well as some design considerations for creating your cleanroom. For in-depth information on designs pertaining to pharmaceutical cleanrooms, review our bio-pharmaceutical cleanroom design guidelines, as well as other helpful articles in our cleanroom learning center.
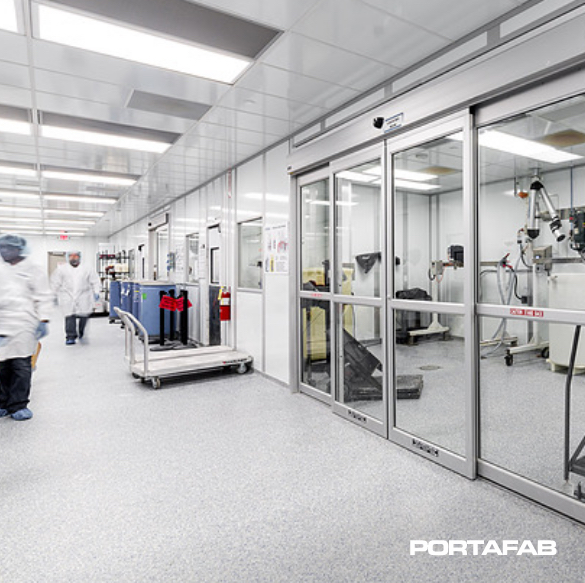
As an industry-leading cleanroom manufacturer, we developed this page to provide information on cleanroom design.

Cleanroom Design Standards
For many companies and organizations, deciding what class cleanroom they need to adhere to is easy - it is specified by a client, government organization or other regulatory entity. For others, the choice can be difficult - so an understanding for how cleanrooms are classified can be very helpful. To assist with this, we turn to the primary authority for cleanroom classifications - the International Organization for Standardization or ISO. They have classifications that range from ultra-clean ISO 1 cleanrooms to ISO 9 cleanrooms that strive to achieve ordinary room air within a dirtier environment.
ISO 14644-1 Cleanroom Standards |
|||||||
Class |
maximum particles / m3 |
FED STD 209E |
|||||
≥0.1 µm |
≥0.2 µm |
≥0.3 µm |
≥0.5 µm |
≥1 µm |
≥5 µm |
||
ISO 1 |
10 |
2.37 |
1.02 |
0.35 |
0.083 |
0.0029 |
|
ISO 2 |
100 |
23.7 |
10.2 |
3.5 |
0.83 |
0.029 |
|
ISO 3 |
1,000 |
237 |
102 |
35 |
8.3 |
0.29 |
Class 1 Cleanroom |
ISO 4 |
10,000 |
2,370 |
1,020 |
352 |
83 |
2.9 |
Class 10 Cleanroom |
ISO 5 |
100,000 |
23,700 |
10,200 |
3,520 |
832 |
29 |
Class 100 Cleanroom |
ISO 6 |
1.0×106 |
237,000 |
102,000 |
35,200 |
8,320 |
293 |
Class 1,000 Cleanroom |
ISO 7 |
1.0×107 |
2.37×106 |
1,020,000 |
352,000 |
83,200 |
2,930 |
Class 10,000 Cleanroom |
ISO 8 |
1.0×108 |
2.37×107 |
1.02×107 |
3,520,000 |
832,000 |
29,300 |
Class 100,000 Cleanroom |
ISO 9 |
1.0×109 |
2.37×108 |
1.02×108 |
35,200,000 |
8,320,000 |
293,000 |
Room air |
(µm denotes micron particle size)
ISO 14644 classifies a cleanroom based on the size and number of airborne particles per cubic meter of air. Prior to the implementation of ISO 14644, Federal Standard 209E set the industry guidelines for cleanroom classification. Both standards are displayed in the above.
Airflow Design Patterns
Another design consideration relates to airflow. To achieve one's required environmental conditions, the air in a cleanroom is purified using High Efficiency Particulate Air (HEPA) filters that can be designed to meet any classification. However, if you also want to control temperature and humidity, recirculating designs are often specified for their more precise control.
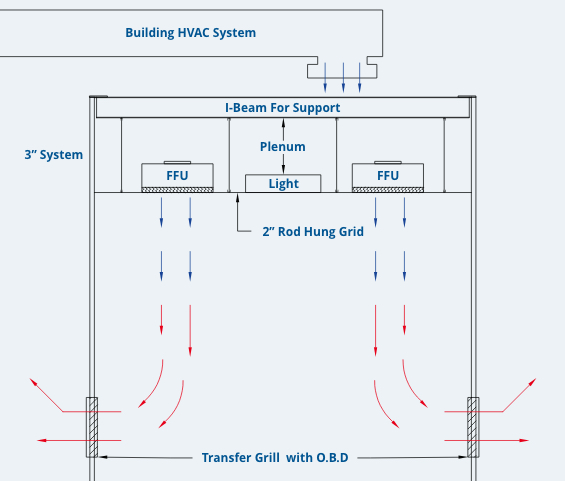
Single Pass Design
In "single pass" design, ambient air is filtered into the cleanroom and transferred out into the surrounding building space.
Single pass designs are commonly used in environments that do not require temperature and humidity control.
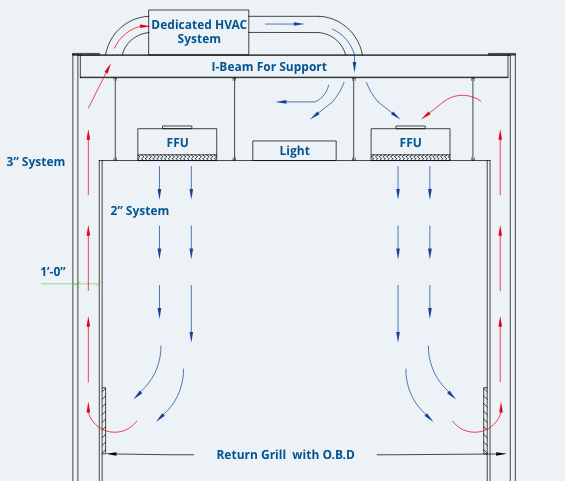
Recirculating Air Design
In "recirculating" air designs, air handling units condition the air, which is drawn through low wall returns and into the ceiling plenum.
These designs are typically used for cleanrooms with temperature or humidity requirements, and to isolate the environment for greater process control.

Design for Flexibility
Flexibly designed cleanrooms can easily accommodate needed expansions as well as modifications that may be required when new equipment or tools are introduced to the cleanroom. This allows changes to the cleanroom to happen rapidly and efficiently, which minimizes the number of contaminants that can be introduced to the room during the exchange process. Additionally, the quick change-over of equipment leads to reduced downtime and increases in productivity. If cleanrooms are designed with expandability and flexibility in mind, the cost of future change will be reduced.
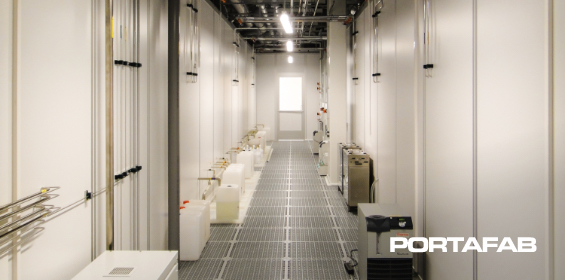
Chase Walls
The chases within walls of pharmaceutical facilities can serve to house mechanical ductwork, electrical utilities, process work, and additional utilities. Due to the amount of services running within the walls, chases may vary in thickness from 6 inches to 12 inches to 18 inches in depth. Access to these chases must be available and allow for future piping expansion capability.
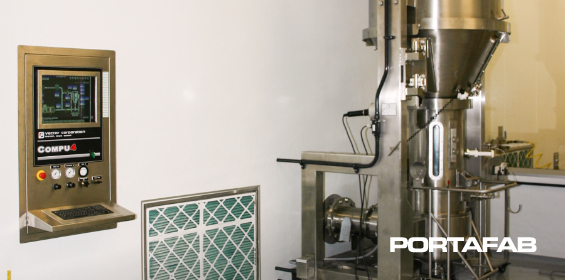
Bulkheads
Since equipment is continually moved in and out of cleanrooms, especially within the microelectronics industry, it’s important that the user be able to penetrate the walls separating bays from chases in any location via bulkhead openings. These bulkheads can be created using components to “box” around the equipment and an extruded gasket can interface with the wall to seal around the equipment.
PortaFab also offers several different wall types that allow you to tailor-make each room to its specific applications. These walls are commonly used for applications such as the creation of electronics, pharmaceuticals, and food goods.
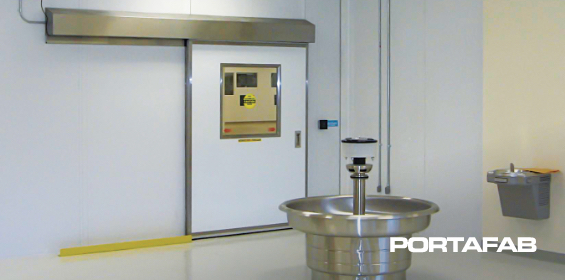
Seamless Walls (where needed)
The seamless-type wall system provides a smooth look and continuous appearance. Seamless-type walls are more critical in biotech and pharmaceutical applications for eliminating crevices in which organic material can grow.
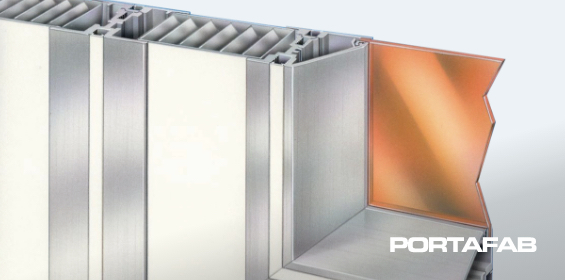
Batten Walls
Most semiconductor facilities experience modifications not only after the cleanroom has been installed but even during installation. The batten wall system provides flexibility and a consistent appearance for in-field modifications.
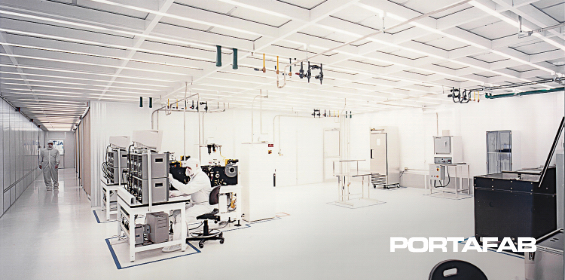
Struts
The ability to support and hang piping and racks from the walls is an important feature for clearing up floor space in the chases. This can be achieved by attaching struts to vertical studs and hanging the lines, and utilizing struts with cavities for additional purposes.

Traditional vs. Modular
When considering the addition of a new cleanroom, there are two methods you can choose: Traditional or Modular. While each method has its own merits, PortaFab focuses on the implementation of modular wall systems to satisfy cleanroom design needs. Listed below are several benefits provided by a modular cleanroom installation.
Cost
Modular installation is often less costly than traditional construction as each component of the cleanroom is prefabricated and simply needs to be assembled once on site.
Alterations
As modular cleanrooms feature a non-progressive construction, they can often be altered easier without the debris and mess that comes with traditional construction.
Expansion
Modular cleanrooms are easy to expand, as the operation only requires adding additional wall, ceiling, and floor systems. Traditional construction may require the demolition of existing walls and systems to make way for new construction.

Choosing a Modular Cleanroom System
It’s important to understand a project’s requirements and separate the required must-haves from the aesthetic nice-to-haves (see table below). The design of cleanrooms and classified spaces requires that architectural finishes be designed to be smooth, easy to clean, non-shedding, and have minimal ledges and joints. Life science applications require radius corners for ease of cleaning, nonporous surfaces, and resistance to microbial and fungal growth. The architectural finishes should also be able to withstand repeated cleaning and sanitizing with various chemical solutions.
Microelectronics |
Life Sciences |
Emphasis on total particulate levels as contaminants |
Emphasis on viable matter as a contaminant |
Concerned with process yields, economic issue |
Concerned with GMP regulatory guidelines |
Concerned with product reliability, functional performance |
Concerned with finishes that can be easily cleaned |
Concerned with static charges as carriers |
Concerned with joints, crevices and recesses |

Common Cleanroom Configurations
Below are four common types of cleanroom configurations that can be used for a variety of different cleanroom applications.
1. Panel-Post Cleanrooms
Panel-post design is a popular and commonly used approach because the systems can be moved, reconfigured and expanded cleanly and easily. Utilizing a nominal 4-foot wide panel with a stud post, the stud post dismantles into two pieces, allowing a panel to be removed without disturbing other panels. All of the components can be reused in new configurations, and raceways built into the system allow easy access to utilities without endangering the classification or causing a rise in particle counts. These systems can also easily accommodate rack-mount utilities on chase walls and bulkhead openings.
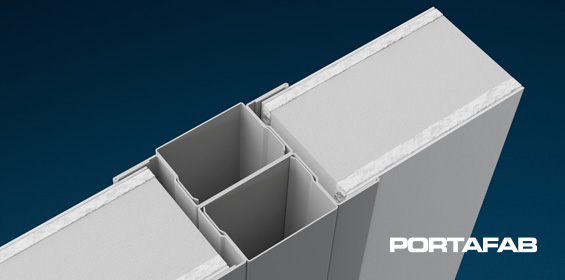
Wide Selection of Materials
A wide variety of smooth materials are available for wall panels and make cleaning easy. Materials include vinyl, melamine, high-pressure laminate, fiberglass reinforced plastic (FRP), PVC laminate, stainless steel or aluminum, and painted steel. Core materials include polystyrene, polyisocyanurate, fiberglass and aluminum honeycomb wall panels. These systems can be designed as freestanding enclosures placed inside of a larger structure, creating a self-contained envelope structure (see image at right). These envelope structures can even be designed with load-bearing decks to support maintenance loads or mechanical equipment.
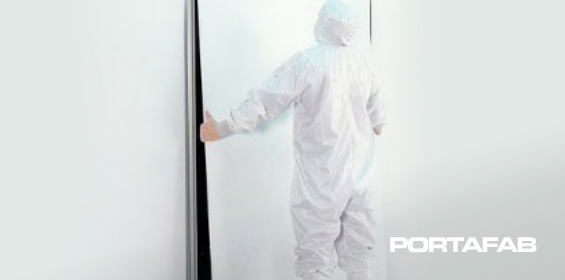
Easy to Modify & Install
The advantages include lower up-front materials cost ($7 to $16 ft2) and complete prefabrication at the factory, minimizing or eliminating on-site cutting. Also, field modifications are easy, and the freestanding structure eliminates the need to reinforce the existing building roof to support equipment and ceilings. In addition, users can apply for accelerated depreciation. The disadvantages are that the joints at stud post locations protrude from the wall about .0625 inch and there are minimal flush-mount accessories (such as doors, windows, grille openings).
Review our CleanLine system for more information and applications of the Post and Panel cleanroom design.
2. Panel-Panel Cleanrooms
Used more within the pharmaceutical arena, these systems can provide non-progressive construction for removal of a single panel without disturbing adjacent panels. Panel edges are formed edges with dog-bone, tongue-and-groove or cam-lock mechanisms to connect a panel directly to another panel, eliminating the ledge of the panel-post design. Joints are sealed with a caulk joint or chemical weld, producing a wall system conducive to wash-down applications. Some systems offer raceways built within the panel itself; otherwise, utilities must be surface-mounted onto the face of the panel or fit-up at the chases. Radius coving at floor, ceiling and corner connections provide easily cleaned corners, and windows and door frames are flush-mount across the plane of the wall.
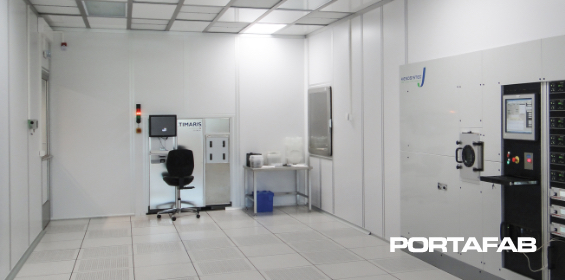
Superior Cleanability
The panel-panel systems are not load-bearing as designed and require an internal support structure or reinforcement at panel joints. The most common surfaces include UPVC-coated steel, stainless steel and painted steel, which can withstand a variety of cleaning agents and exposure times. Cores include polystyrene, fiberglass and aluminum honeycomb.
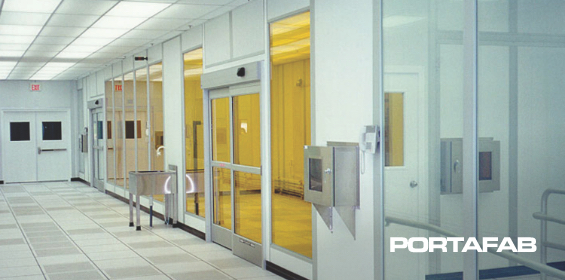
Advantages - Disadvantages
Advantages include complete prefabrication at the factory, minimizing or eliminating on-site cutting, and minimal ledges and joints, producing an easy-to-clean surface. Also, they offer good aseptic detailing and radius coves, and users can apply for accelerated depreciation. Some disadvantages are the higher material costs ($22 to $30 ft2), the expense of double-chase walls for utilities and returns, and field modifications are more difficult due to the finished vertical panel edge.
Chases can be created in both the freestanding panel-post and panel-panel designs by installing a double run of wall, creating the chase wall on either side of the utilities. This can become an expensive design, however, depending on the panel construction used.
The double-wall approach has been seen as a more cost-effective approach because:
- The metal stud framework provides support and a means of attachment for utilities and processes.
- The panels supported off the metal studs on both sides are thinner and occupy less space within the cleanroom.
- Double-wall panels on metal studs are less costly.
- Contractors can frame out the metal studs up front and install utilities prior to panels arriving.
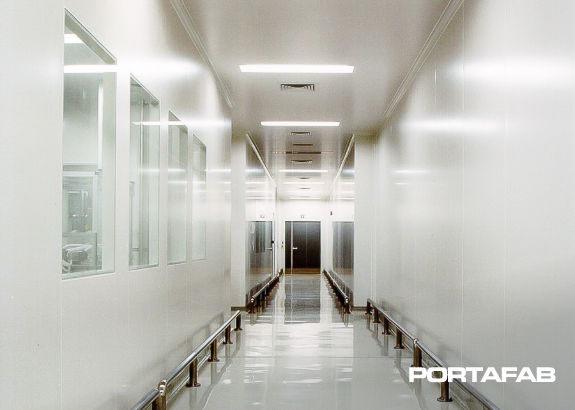
Review our Fabline Clean Room Wall System for more information and applications of a panel-panel design.
3. Double-Wall Cleanrooms
Double-wall clean room designs offer a unique solution for pharmaceutical applications. These systems integrate with a metal stud framework by hanging off one or both sides of the studs, creating a utility chase with a more economical panel. Panels have formed or cut edges to connect panels directly to one another and they utilize a caulk joint, gel coat or chemical weld, creating a smooth panel transition across the surface of the wall. Individual panels can be removed by striking the joints and removing the panel from the framework. Panel thicknesses are between 0.50 inch and 0.625 inch, and can provide an alternative to creating a chase wall from two thicker panels, which can be very costly. The use of a metal stud framework can also provide separate utility and electrical support and panels can be prepped for all fit-ups.
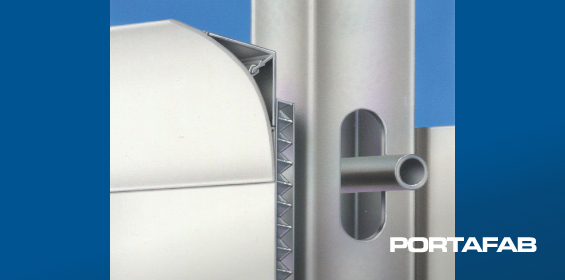
Flush Mounting - Free Standing
Easily cleaned radius covings are provided for all connections, while doors and windows are an integrated part of the system for flush-mounting into the walls. Freestanding envelopes can be created by using structural metal studs or columns within the chases to carry beam loads.
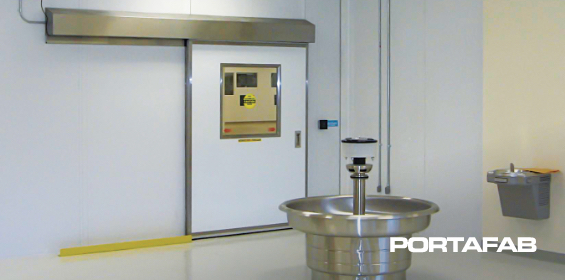
Several Surfacing Options
A wide range of surfaces are available for these systems, including fiberglass-reinforced plastic, stainless steel, glassboard, painted steel or aluminum, and PVC-coated steel-all of which are chemically resistant to aggressive cleaning agents. Core materials include aluminum honeycomb, XP board and gypsum.
4. Furring Wall Cleanrooms
Furring wall systems can be attached to any solid wall or wall surface, including block, concrete and drywall. These systems are a good solution for upgrading existing areas in lieu of using a full freestanding panel, which can be very costly.
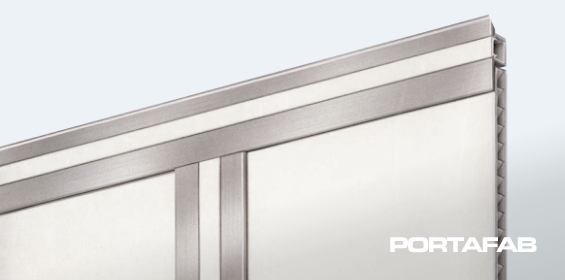
Multiple Attachment Options
There are various attachment methods for securing panels to existing surfaces. Wall systems for microelectronic applications generally use an extruded aluminum batten every 4 feet between vertical panel edges and have concealed fasteners.
Pharmaceutical systems may use a hanging “Z” clip attachment, which supports the panels and provides formed or cut edges in conjunction with a caulk joint, gel coat or chemical weld, creating a smooth transition from panel to panel.
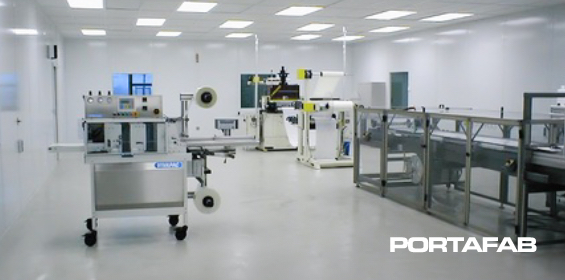
Fire-Rated Perimeter
Spaces requiring a fire-rated perimeter often use a furring system to finish off walls with a cleanable, non-shedding surface. Column enclosure also benefits from using a furring system to finish onto drywall or to create return chases with strut or metal studs.
Panel thicknesses of 0.25 inch to 0.625 inch are available with painted aluminum or steel, fiberglass-reinforced plastic, stainless steel, and PVC-coated steel. Core materials include aluminum honeycomb, XP board and gypsum.
Review our Fabline Furring Wall System for more information and examples on Furring wall designs.

Additional Cleanroom Components
Do you want to know about the additional types of cleanrooms, or the various components that can be added to ensure that your processes, products, and technicians are ISO compliant?
PortaFab’s Modular Clean Rooms
Modular cleanrooms provide an excellent alternative to traditional construction methods. They are simple to install, require no cutting, create no debris, and can be relocated with ease giving your operations a degree of versatility that a permanent-non moveable construction would not be able to offer.
Clean Room Components
Cleanroom Operations often consist of several different cleanroom components working simultaneously to ensure that processes or products are protected. If your cleanroom requires additional components, PortaFab has several different solutions that you can use to enhance your build.
Cleanroom Construction Expertise
For over 40 years, PortaFab has been helping organizations with all of their clean room and environmental control needs. Our staff of design consultants work with architects and general contractors to deliver functional and cost-effective solutions, resulting in a smooth and quick cleanroom construction process.
PortaFab’s Cleanroom Learning Center
Do you have more questions regarding cleanrooms or controlled environments? PortaFab’s Cleanroom Learning Center has several resources that can help answer your questions.