JUMP TO: Sandwich Panels | Aluminum Honeycomb Panels
PortaFab manufactures standard and custom composite panels for interior applications in prefabricated modular construction systems. These composite panels consist of multiple layers, such as aluminum, steel, and insulation cores, bonded together to create a lightweight yet sturdy product. PortaFab uses high-quality materials and in-house machinery to meet rigorous standards for strength, durability, and thermal insulation.
PortaFab customizes composite panels to meet specific client needs, including size, finish, and color options. Designed for easy integration into modular construction systems, these panels allow for quick assembly and disassembly, ideal for interior applications like cleanrooms, modular offices, and partition walls.
With features such as fire resistance, soundproofing, and thermal efficiency, PortaFab's composite panels enhance the functionality and comfort of interior spaces while maintaining aesthetic appeal. This approach improves construction efficiency and ensures long-lasting performance in various settings.
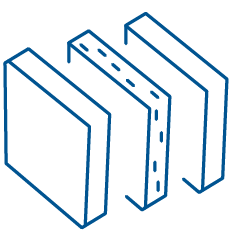
Composite Panels
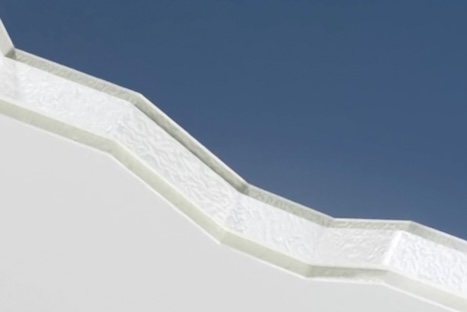
Sandwich Wall Panels
Choose from dozens of core materials, surfaces, and edge closeouts to create the perfect panel for your application.
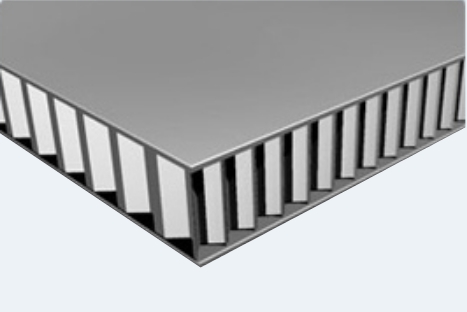
Aluminum Honeycomb Wall Panels
Aluminum honeycomb panels, customizable in size, aluminum grade, material depth, and wall thickness, offer lightweight, high strength, moisture and corrosion resistance, excellent thermal conductivity, non-combustibility, and high resistance to fungi.