A global biopharmaceutical company that produces specialty pharmaceutical products including generic drugs and imaging agents to various countries worldwide. They required the installation of a new environmentally controlled sampling booth in which to sample incoming API’s (active pharmaceutical ingredients) within a clean environment, free of contaminants in order to preserve product quality. After inspection, incoming goods would need to be repackaged within the environment, then removed for storage outside of the enclosure.
Our distributor provided the biopharmaceutical company with a new product sampling booth at their manufacturing facility located in Illinois. The enclosure would provide their client with a temperature and humidity controlled area in which to inspect and re-package incoming products to ensure product quality.
Project Overview
Application: Product Sampling Booth with Temperature and Humidity Control
Product: Cleanline S3000 Wall System with FRP Wall Panels
Benefits Provided:
- Met requirements for ISO 8 and ISO 7 level classifications
- Compliance to EU Standards
- Integrated controls for High speed and conveyor system to create automated process
- Dedicated HVAC system to maintain temperature and humidity requirements
The Challenge
Our client previously had been using a portable soft wall cleanroom to perform its API sampling. Due to increased quality control measures as a result of marketing a new product overseas, our client needed a new facility built to meet EU standards.
Due to its existing relationship our dealer had with this client; our dealer, through past project success worked with PortaFab’s engineering department to specify the requirements and receive approval from the client to build the new sampling room.
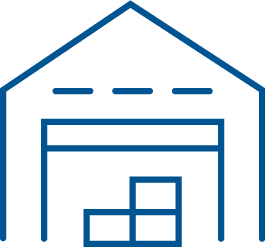
The Solution
The finished enclosure consisted of a standalone HVAC system to support the interior ISO requirements of the ante room and sampling room. Both rooms featured Fiberglass Reinforced Plastic wall surfaces for greater cleanability and reduced contamination. Lastly, the enclosure featured high-speed roll up doors at both entry and exit ends of the structure for improved environmental control.
The entire structure integrated with a conveyor system to provide a completely automated process. A high-speed roll-up door allowed products a quick entry into the airlock room for minimized contamination. The interlocked high speed doors provided consistent temperature control and minimized contamination for a quality testing and repackaging process. Afterwards, the conveyor system moved the product back outside of the chamber and towards a dedicated storage area. This type of integrated automation improved throughput within the facility in addition to meeting the higher quality control standards required for the new product introduction overseas.
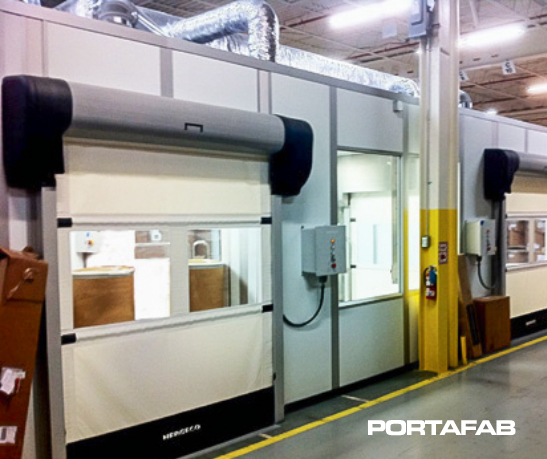