Based on a positive past working relationship with this client, our dealer was selected to improve the storage capacity of an existing warehouse. After consulting with PortaFab engineering, our dealer proposed utilizing a mezzanine design for this project.
A global equipment technology company required the help of our dealer in order to optimize the existing space at their Colorado facility. The client had recently merged their operations and inventory branch with their service branch in Colorado Springs, requiring the facility to accommodate additional square footage under one roof. Our client reached out to our dealer for a solution based on their trusted working relationship which had been established through our dealer’s solid performance of past work.
Project Overview
Application: Mezzanine Storage and Laboratory Space
Product: OmniFlex Fire and Sound - Gray
Benefits Provided:
- Expanded vertically by incorporating a mezzanine design.
- Storage solution adhered to local fire code and did not require expansion of existing facility.
- Ability to reconfigure layout and adapt to future business changes or expansion.
- Turnkey solution featuring fire suppression, HVAC, lighting and engineering & building permits.
The Challenge
To create additional storage space, the client originally considered a stackable storage option. However, local fire code would not permit stacked storage units to exceed 12-feet high within the current facility, so a simple stacking of inventory would not suffice. The client wanted to avoid having to renovate their existing facility through traditional construction means, and instead, hoped to utilize a more flexible alternative that could accommodate future business changes or expansion.
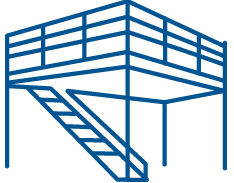
The Solution
After consulting with PortaFab, our dealer presented the solution in the form of a 7,000 square foot mezzanine design. The lower portion of the mezzanine would integrate with PortaFab’s modular wall panels to create a large laboratory, which could be used for equipment service and repair. The top floor would provide the storage space required for their inventory needs. The modular components provided a degree of flexibility, allowing the walls to be expanded or re-arranged, based on future needs.
The completed mezzanine and laboratory space provided an optimal solution for the client. The close proximity of the repair lab and stored inventory allowed greater efficiency between both departments, who, in the past, had to travel between two independent facilities.
The resulting structure provided our client with a complete turn-key solution that included associated fire suppression, HVAC, lighting, and adherence to local engineering and building permits – All completed on time and within budget.
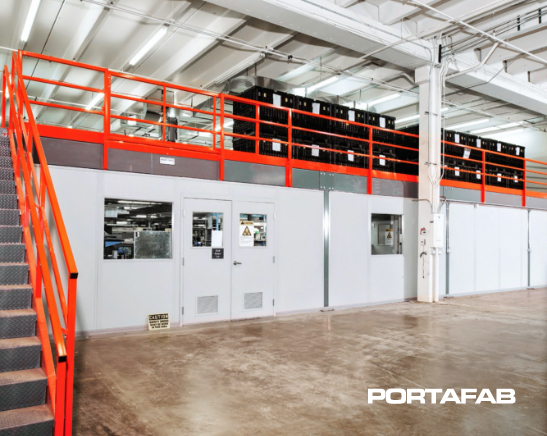