Federal Standard 209 in its several revisions (A through E) has been used for more than 30 years as a guide for cleanroom designers. An industry has been founded on the directive, "to be in accordance with Federal Standard 209". The standard has been quoted and misquoted in the interest of describing a clean space, clean air, clean products, clean processes, and clean materials, to name a few items. The intent of the standard has evolved to the point where at this time it defines clean air in the English and metric systems and describes how to measure that level of cleanliness.
There is currently a movement afoot to replace this document that has defined the cleanroom industry in the United States, and in truth, in many parts of the world, with a document created by the International Standards Organization (ISO). This movement is an international effort in which the U.S. has participated and which has resulted in a multiple part document that in the opening years of the millennium may very well become the guiding document for cleanroom design in the U.S. and throughout the world.
ISO 14644 Cleanrooms and Associated Controlled Environments will most likely become very familiar to those of us who design Cleanrooms. How will it affect what we do?

The American Way
Design of cleanrooms in the U.S. has evolved from a somewhat sophisticated, if not necessarily uniform, application of accepted procedures. The backbone of the available documentation has been Federal Standard 209, which defined air cleanliness in terms of numbers of particles of a particular size per unit volume. The earliest version identified class 1000, for example, as being the number of particles of .5 microns size and above, in a one cubic foot sample of air. This became a bit more obscure in recent years as class 1000, in our metric form, is expressed as class M4.5. The standard also dealt with particle count measuring techniques.
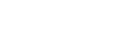
INSTITUTE OF ENVIRONMENTAL SCIENCE AND TECHNOLOGY (IEST)
The Institute of Environmental Science and Technology (IEST) developed a number of useful recommended practices (RP's) for proper cleanroom design. These provided cleanroom designers with specific documentation that could be referenced at multiple stages of the design phase to ensure all recommended procedures were completed.

"NON-STANDARD" PRACTICES
Companies with leading edge contamination control programs developed design parameters and frequently design methodology that, while effective, might be at odds with the IEST RP's, but were regarded as effective and were made mandatory for that company's cleanrooms. As designers moved from company to company these "non-standard" practices moved as well, and over time came into more or less common use.

THE FINAL ANALYSIS
In the final analysis, the design approach, cost, operating characteristics, design features, etc always were a matter of agreement between the buyer and seller. While the document described above may have been referenced in some fashion, they only took on the cloak of "law" when buyer and seller agreed. That's the AMERICAN WAY.
Cleanrooms & Associated Controlled Environments (ISO 14644)
Indicated below are seven parts of the ISO document that will govern how cleanrooms are identified, designed, constructed, tested, and operated. As this is written all but Parts 1 and 2 still have to go through the approval stages of ISO document adoption.
- Part 1. Classification of Air Cleanliness
- Part 2. Cleanroom Testing for Compliance
- Part 3. Methods for Evaluating & Measuring
Cleanrooms & Associated Controlled Environments
- Part 4. Cleanroom Design & Construction
- Part 5. Cleanroom Operations
- Part 6. Terms, Definitions and Units
- Part 7. Enhanced Clean Devices
- Part 8. Molecular Contamination
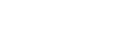
Part 1 and 2
Part 1 and 2 have been adopted and published. The other parts are out and about, and while not formally adopted, are being used to a lesser or greater extent as cleanroom designers and end users discover their existence and strive to be "on the cutting edge" of the technology.
This Supplement deals with cleanroom design and construction issues and will therefore address Part 4 in some depth, particularly as it affects current cleanroom design practice.

Part 4
Part 4 is divided into two parts and have been labeled "shall" and "may". The "shall" section contains those elements of cleanroom design and construction that must be present in a facility to enable it to bear the label "designed and built with accordance with ISO 14644". The "may" part describes some specific examples of cleanroom design and construction practice that might be helpful to the reader but need not necessarily be incorporated into the design if an alternate practice would be similarly effective. The "may" part of the document is in the form of a series of annexes.
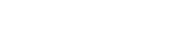
THE ISO WAY (THE "SHALL PART")
The "shall" part calls for procedures which, if properly created and carefully followed, cannot help but result in an outstanding cleanroom project. But the creation of the procedures and the responsibility for implementing them is left squarely on the shoulders of the cleanroom designer. Those who feel that this new ISO standard is going to eliminate the need for the design professional can rest easy. The engineering challenges are still in place. ISO does not take away design freedom, although through its' Annexes it may offer suggestions (the "May" part).
One thing that ISO 14644-4 does not demand is a sense of order that should be present in any well-conceived project, but frequently may be missing. All the elements that a well-organized engineering office would impose on a project are required if the end result is to bear the ISO label. ISO discourages cost cutting schemes that circumvent the process. There may be a positive and a negative to this but it will definitely prove to be a change to some designers and clients.
A final note regarding terminology: The European influence is present throughout the document due to Europe's extensive experience with pharmaceutical based cleanrooms. Cleanroom groups in the U.S. tend to have more of a microelectronics industry flavor and the documents reflect this. The combined jargon should not be an obstacle but it may require the reader to reflect on the intent of a statement a bit longer than usual. Ultimately the intent of the writers is quite apparent.
Specification of Requirements
|
ISO 14644-4 requires that there be a formal agreement between the designer/builder of the cleanroom and the buyer. This agreement will identify the parties involved in the project and describe their role. It will describe the duties, authority and responsibility of an engineer, architect, consultant, builder, etc. There should be no doubt at the beginning of the project about "Who does what." |
|
The environmental parameters such as cleanliness class, temperature, humidity, sound level, etc with appropriate tolerances are to be specified for each space. The ISO 14644-4 Annexes offer some guidance for microelectronics, pharmaceutical and some other applications but ultimately final specification is left to agreement between buyer and seller. |
|
The layout of the facility, including the size and shape of prominent areas, including gowning rooms, airlocks, air showers, and pass-thru boxes should be determined. The manner of which cleanliness is to be maintained should be understood. Whether unidirectional, vertical or horizontal flow, the scheme should be understood by seller and buyer. |
|
The test program should be designed to prove the seller has met intent of the buyer. "As built", "At rest" and "Operational" modes, a carryover from Fed Std 209, should be detailed. |
|
The flow of personnel and materials in and out of the facility, including types and numbers of doors, should be described. |
|
Maintenance services and warranty information should be included in the original project scope. Any routine ongoing maintenance should also be identified. |
|
The external environment of the clean space should be defined. That is, will the cleanroom be within a conditioned building or what will be the environmental conditions surrounding the cleanroom? What is the source of make-up air? Can the building roof support a ceiling load or air conditioning equipment load? |
Perhaps as important as any element of the ISO specification requirements is the acknowledgment that the cleanroom may house process equipment which can produce excess heat, waste water or exhaust gases. Developing a utility matrix is important and mandatory if ISO 14664 is being followed.
The experienced cleanroom designer/builder and buyer will see that there is little new here. Rather it is an acknowledgment that all the bits and pieces that found their way into a cleanroom contract in the past are now mandatory if the facility is indeed to be compliant with the ISO standards. These standards are a starting point around which comprehensive specifications of requirements will be developed.
The Planning Procedure
A quality plan consistent with industry standards and incorporating ISO standards where appropriate is required. The requirement for a plan is basic to any project. The specific elements required by ISO 14664 are not detailed in a manner that should restrict the creative juices of the designer or buyer. The intent is to identify issues for the buyer and designer to address and upon which to reach an agreement prior to the construction phase of the project.

The ISO standard calls for a project plan that includes design documents with supporting calculations as well as a project budget and schedule.

Other elements that comprise the planning process include the identification of risks associated with meeting budget and schedule goals, as well as a review of design alternatives with a statement of positive and negative features.

The plan should include an evaluation of maintenance requirements; a statement as to the need for flexibility and a discussion of how such flexibility is provided; a statement regarding the need of redundancy and how stand-by capacity is provided; and a review of project constructability and to ensure the design will support the construction schedule.
Construction and Start-up
"Plan the work and work the plan" is reinforced by ISO standards: The need for a change in process is identified. Changes to the "plan" are then discussed, agreed to and documented before the changes are implemented.
A clean construction protocol is required, however, the elements of the protocol are not defined. In essence, this section calls on the parties involved in the project to recognize the need for "building clean" and then devise a protocol that is agreeable to all parties.

The need for cleaning during the course of construction and at the completion of construction activities is emphasized. ISO calls for a specific procedure here as well, while the elements of the procedure are left up to the discretion of the project parties.

The need for testing to insure that the cleanroom components are functioning properly is required. In addition, specific reference is made to training operating personnel during system start-up.
Testing and Approval
Those familiar with bio-pharmaceutical validation procedures may see that influence in this section. Construction approval is intended to convey that the intent of the design and the letter of documentation (or plan) have been followed. A series of check sheets might be an appropriate way of documenting the "pass-fail" criteria established during the planning stage in this continuous inspection procedure.

Functional approval suggests a series of tests in the "as built" or "at rest" modes described in Fed STD 209. The intent is to determine that all components function as intended.

Operational approval is achieved when the cleanroom is in full operation, that is, when all process equipment and personnel are actively pursuing assigned tasks, and the cleanroom continues to meet design intent.
Documentation
ISO procedures have the reputation of being long on paperwork. ISO 14664 upholds this reputation with its requirement for extensive documentation. Installation documentation includes as-built plans and specifications along with test data and spare parts lists. Reference to such documentation some time after the facility has been completed should provide accurate information that can be used for facility upgrading, troubleshooting, or repair.

Operation instructions include the acceptance test procedures, "pass-fail" criteria and test data that can provide a baseline of performance of the facility against which current data can be measured.

In addition to "start-stop" instructions under normal conditions, emergency situations should be covered as well as procedures to be followed in the event of a component failure. This is particularly important should life safety be involved. Performance monitoring instructions describe the variables to be monitored. Normal/alarm limits are defined as action to be taken in the event of an alarm situation.

Protocols are required for periodic and emergency maintenance. Inherent in such protocols are safety issues relative to equipment repair or replacement. Records of operational data and periodic test data taken, and maintenance procedures performed are required. ISO acknowledges the role of operating and maintenance personnel and requires records kept on training programs and recipients of such programs. Note that here again those familiar with biopharmaceutical installations may find these issues routine while they may be new to users of cleanrooms in other industries.
The ISO Way (The "May" Part)
ISO-14664-4 contains a series of Annexes that offer guidance in a manner similar to the "non-mandatory" section of the "B" revision of Fed Std. 209. One reason this section was dropped in subsequent versions of the federal standard is that the guidance presented slowly became the basis of specifications and in practice became mandatory. It remains to see if these advisory sections of the ISO document have a similar suffocating effect on cleanroom design.
In a style reminiscent of the IEST, Recommended Practices and Annexes deal with contamination control zones and airflow patterns (unidirectional, non-unidirectional, and mixed airflow). Some typical applications are discussed along with "examples" of air velocities found in cleanrooms of specific ISO classifications.
Some of the seemingly vague directives of the "shall" part of the document are fleshed out with examples of checklists and more details of what constitutes a review or approval process for those seeking guidance in this area.
Much of the "Shall" part of the document is generic in that it might apply to any type of construction. The Annexes get specific about "cleanrooms" and several give descriptions of typical cleanroom areas, their functions, and how they relate to the whole. Material of construction for floors, walls, and ceilings as well as other components and other construction considerations are presented in sufficient detail to illustrate the uniqueness of the cleanroom.

Environmental Control of Cleanrooms
The Annex on environmental control of cleanrooms emphasizes the complexity and variety of these concerns in cleanroom design. The key parameters are described in somewhat limited detail with the caveat that different applications have different requirements. The value of the Annex is as a checklist to insure that appropriate issues have been identified and analyzed. The sample parameter value ranges presented are sufficiently broad to permit design flexibility. The suggested range of sound value may create some mischief as a 40-65dB (A) may be satisfactory on the high end but the low end will be significant engineering challenges.

Control of Air Cleanliness
The Annex on control of air cleanliness is sketchy at best but at this point in the evolution of cleanrooms sufficient information is available from other sources to suggest this treatment is adequate.

Facilitate a Clear Understanding of Requirements
The final Annex has a stated purpose "to facilitate a clear understanding of requirements." It does so by presenting page after page of process related factors to be considered as well as environmental safety, standby, operational and maintenance factors. The listing presents useful information but more importantly addresses the need for thorough communication between designer and end user if the cleanroom project is to be successful.

International Consensus Document
This document addresses on an international level those issues that individual countries have been addressing over the years relative to cleanrooms. It is an outstanding first cut at an international consensus document. While, frankly. There is nothing really new here; the weight of ISO is behind "good engineering practice". Such practice is no longer optional.
Cleanliness Class Comparison
The ISO standard introduces a new array of cleanliness classes. The simple designation of the early U.S. Federal Standard 209 wherein a class number was a statement of the number of .5 micron particles per cubic foot of air is gone. The "M" for metric classification has also disappeared. The new classifications numbers, defined in detail in ISO14644-1, start at 1 for the most stringent and go to 10 for the least stringent. It will take some getting used to for those classification numbers to fall from the lips of the same manner as the old family Class 100 or Class 100000 designations, but as our world strives for uniformity and as the metric system gradually replaces the English system we will have to learn to be comfortable with the new designations.