The client is a manufacturer of rugged tubes, hoses, and fittings used in natural gas processing, hospitals, and manufacturing plants. After receiving a $2.3 million investment, the client decided to consolidate some of its research efforts in high-tech polymers from labs in Europe and the U.S. The client required a new Cleanroom to be constructed within their facility in order to aid their polymers research program. PortaFab’s Cleanroom product line was specified by the client due to previous successful projects with PortaFab and the client's base in the US.
Project Overview
Application: Cleanroom (ISO 7 & ISO 8)
Products:
- Series 300 aluminum framing system
- Vinyl Fire & Sound Panels
Benefits Provided:
- Multiple ISO classifications for different areas including gowning room, temperature-controlled storage area, and main lab.
- High visibility windows to serve as client demonstration area.
- Complete turn-key solution through PortaFab’s involvement with general contractor, pre-construction meetings and on-site supervision during installation.
The Evaluation
The Cleanroom enclosure would require multiple rooms, including a gowning room, main laboratory area as well as a storage area for the polymers. Strict environmental control would be required in order to maintain safe storage and handling of the polymers including temperature, humidity and reduction of particulates.
The client also requested the addition of high visibility windows to be utilized with the Cleanroom environment to serve as a demonstration piece for visiting clients.
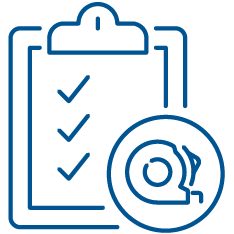
The Solution
Our distributor worked closely with PortaFab’s engineering and design team throughout this project to ensure that expectations were met based on our previous working relationship with the client. PortaFab also worked closely with the Cleanroom contractor from initial specification throughout the Cleanroom construction to ensure specifications were met, which included attending pre-construction meetings and on-site supervision during the installation process.
Our distributor utilized our Series 300 aluminum framing system featuring 12-foot tall walls with our Fire & Sound panels to provide the required level of thermal control. Based on our client’s request, our distributor incorporated full length glass window panes to the exterior two sides of the Cleanroom to provide full views of the process inside. The attached gowning room was designed as an ISO 8 classified area, while the main laboratory space featured a recirculating Cleanroom design and an ISO 7 classification.
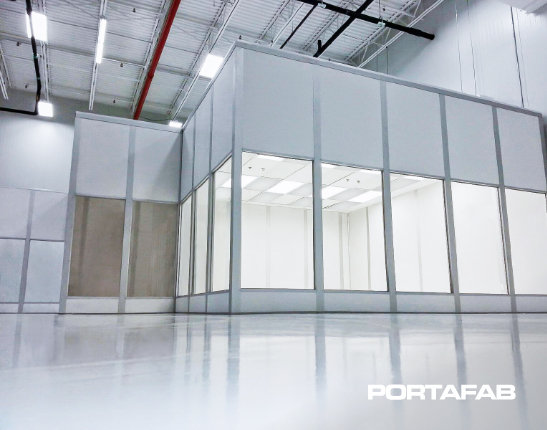