The client is a developer, manufacturer, and worldwide supplier of precision-engineered o-rings used in a variety of industries from automotive to semiconductor processing. They reached out to a PortaFab Cleanroom contractor to discuss the installation of a Cleanroom enclosure at their manufacturing facility.
The new Cleanroom environment would contain multiple rooms, separated, in order to facilitate clean manufacturing at each stage of product development, including initial compound mixing to molding, washing, and final packaging of the product. The entire Cleanroom facility would need to be designed to meet an ISO 7 (Class 10,000) classification in order to meet the standards and requirements in place for manufacturing this particular product.
Project Overview
Application: Cleanroom ISO 7 (Class 10,000)
Product: Series 300 with FRP Fire & Sound Panels
Benefits Provided:
- A complete, turn-key solution through PortaFab’s existing network of Cleanroom contractors.
- Multiple clean environments in which to contain each stage of the manufacturing process from initial mixing to product packaging.
- ISO 7 (Class 10,000) classification featuring recirculating design and positive pressure.
The Evaluation
The facility would need to maintain positive pressure, featuring a recirculating airflow design with the air circulating at 60 times per minute. The wall systems used would need to provide enough durability to stand up to regular wipe downs and cleaning protocols as well as house equipment pass-throughs to ease the transfer of the final packaged products out of the Cleanroom.
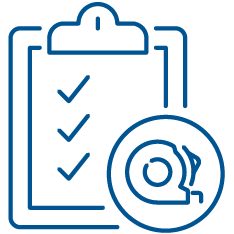
The Solution
PortaFab was able to supply a turn-key solution for the client and successfully upgrade the existing non-clean facility into a converted space housing multiple clean environments.
The Cleanroom complex consisted of two 3-wall structures on either side of an existing concrete wall to form one large environment (40’6” x 32’ x 12’ tall). Our distributor utilized a composite panel as an economical solution to clad both sides of the existing concrete wall and fully contain the environment inside.
Our Series 300 product line was used to construct the rest of the enclosure and multiple interior rooms based on its ease of cleanability and appearance. The fiberglass reinforced plastic (FRP) panels offered the durability required in order to withstand the repeated wipe-down and cleaning protocols required.
Our client was extremely impressed with our distributor’s work and the look of their new Cleanroom. They later referred our distributor to a client who requested a similar enclosure to be installed at their manufacturing facility.
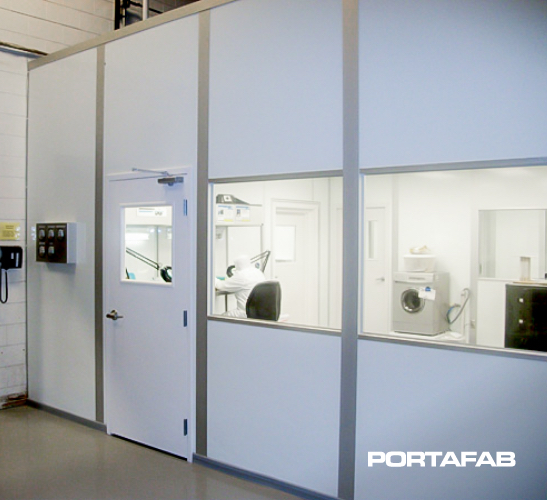