Our client, a manufacturer of intricate electrical components, relays and circuit-boards for automotive and other industries, was giving itself a strategic facelift to prepare itself for a bright future. One of the results of this shift involved rearranging the plants for more efficient and cleaner manufacturing.
Enlarging their automated operations at the 110,000 square foot facility meant moving many of their manual assemblies to one of their other locations. The few labor-intensive jobs remaining in this location had to be segregated from the sensitive robotic equipment taking over much of the plant.
Project Overview
Application: 270' Long x 21'-24' tall graduated wall to divide plant space
Product: XTRA TALL Wall System
Benefits Provided:
- Protect sensitive machinery
- Improve appearance of plant to visitors
- Increase space utilization
The Challenge
The client needed to segregate the contaminate-producing functions within their warehouse while keeping a high-tech image and ensuring their position as a world-class operation.
The tooling manager for the client commented on the strategic reorganization of the plants, "The way the plant was set up didn't fit, so we decided to make a move to make it fit. We divided our plant up to move our manual assemblies and our support group across the hall."

The Evaluation
Systematically separating the sound, dust and other contaminants from the automated equipment was a lot more difficult than just packing up and crossing the hall. The client had to make sure that the divider stretched the length of a 270 foot area and reached a 21-24' foot tall ceiling cluttered with joists, pipes and hoses. It also had to accommodate a variety of pass-throughs, doors, and windows.
It was determined that the PortaMax XTRA TALL wall system was the solution needed to meet the client's complex specifications. It provided the flexibility to effectively divide the client's plant with its pre-engineered panels customized to fit around the existing obstructions and its non-progressive construction allowed for easy expansion or alteration to fit the client's future needs.
"It's difficult to put a price on the new, clean look, but it definitely is worth a lot. We have many more customers visiting us and everyone is very complimentary of the appearance of the structure."
- Client Testimonial
The Solution
The client considered drywall and looked at a few different modular options, but PortaFab could provide the quality, flexibility, service, and high-tech look at a better value than others. Plus, the PortaMax demising walls provided excellent sound reduction and non-combustibility that other options did not provide.
The PortaMax pre-engineered panels arrived ready for fast and easy installation with minimal plant disruption ensuring continuous flow of operations in the facility. The sheer size of the project required consistency of appearance and PortaFab's extensive line of panels, posts, window systems created the uniform look not achievable with drywall or other competitive modular systems.
Our PortaMax system not only met the client's need for warehouse segregation - it also met all of the requirements for environmental control, increase space utilization and improved appearance.
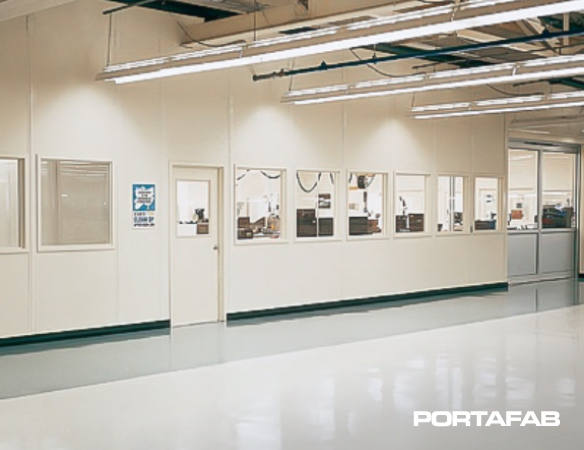