Our client, based in Pennsylvania, is a leader in metal packaging for the food, beverage, household, industrial, health and beauty industries. The company manufactures cans, closures and other aerosol, beverage, food and specialty packaging items that are made out of metal.
The company needed to construct an isolated modular cleanroom that would comply with EPA regulations related to VOC's in the air generated by its baby food can lid printing and manufacturing room. Our client is committed to the environment and green initiatives so the company explored the benefits of modular construction vs. traditional construction methods.
Project Overview
Application: 22' to 28' demising walls to create packaging enclosure
Benefits Provided:
- Divided packaging area from the rest of the facility.
- Contained noise and particles.
- Operator could oversee production from outside of packaging area.
The Challenge
Within the room, there were three assembly lines where pallets of sheet steel were loaded into press auto feeders, multi-color printers, bake ovens, stamp-out presses and bulk box unloading areas. The largest production line was 45 feet wide and 78 feet long. This meant that PortaFab had to create a 3,510 square foot room that also had 22 to 28 foot ceilings and everything in the room had to be completely contained.
Because of the size of the space, constructing a traditional built wall would be extremely labor intensive and inconvenient to ongoing operations. Modular systems on the other hand could be brought in and constructed much more quickly. Plus as the company adjusted the operation in the future, modular systems could be re-purposed. As a result, our client decided to utilize modular systems to create the demising walls.
The Solution
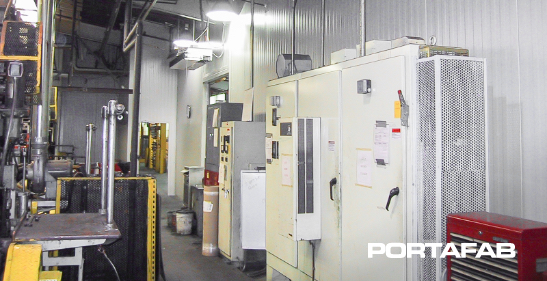
Wall Systems
In order to create the enclosures, the wall system would need to expand up to 28 feet high in order to create a thermal seal from floor to ceiling. High speed doors would need to be integrated into each enclosure for quick entry and exit of warehouse vehicles while maintaining environmental control.
PortaFab supplied its local dealer with the materials needed to properly complete this project. The dealer recommended the SteelSpan floor-to-roof wall system, which measured between 22' and 28' tall. The main roof's HVAC and burnoff system were able to contain the toxic solvents so that additional ventilation systems were not needed.
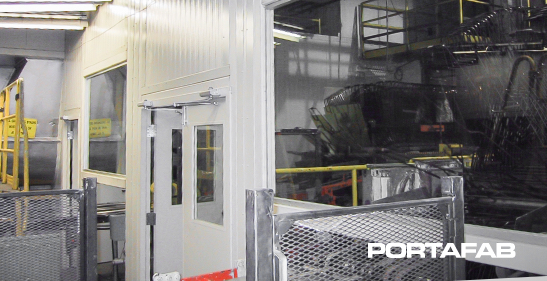
Specialized Features
PortaFab designed the room with several specialized features:
- Windows were added in the walls so equipment control panels could be placed outside of the room, enabling operators to avoid breathing in the VOCs at all times.
- Conveyor openings were cut into the walls to facilitate easy pallet loading.
- The installation of double doors ensured accessibility for future equipment maintenance.
Although the purpose of the wall system was VOC containment, it also provided a sound barrier so that the noise levels from the printing processes were not as pervasive.