Due to recent company growth and in light of pending regulations by the FDA governing e-cigarette and e-liquid manufacturing, our client wished to improve their manufacturing standards by complying with current GMPs and the anticipated FDA regulations.
Though this client already possessed a stick built cleanroom within their facility, they had been experiencing tremendous growth and needed a larger clean environment to house their expanding e-liquid manufacturing processes. This client was already familiar with modular construction due to an existing PortaFab office within their facility. Realizing the flexibility and speed at which modular structures could be installed, they contacted PortaFab to discuss a potential modular solution.
Project Overview
Application: E-Liquid Manufacturing Cleanroom
Product: OmniFlex Two-Story Building
Benefits Provided:
- Provided a clean environment that met ISO 6 (Class 1,000) classification.
- Fast and low mess installation allowed client to maintain manufacturing progress, uninterrupted during the new construction project.
- Flexibility to expand or even re-locate the building due to future growth or changes in business needs.
The Evaluation
Our distributor took the time to meet with their client over several weeks to discuss a wide range of solutions while also evaluating their client’s needs, which included the desire to be up and running quickly after installation. Our client also appreciated the flexibility inherent in utilizing modular systems as they were experiencing recent growth and may need to expand their facility again in the near future.
In addition, being a growing company in a leased space, our client appreciated the tax benefits and the ability to completely re-locate the new cleanroom into another facility if future needs changed. All of these benefits resulted in the client accepting our distributors proposed design and signing off on the cleanroom installation.
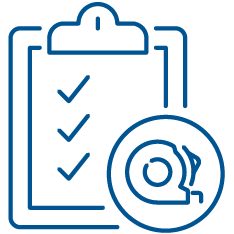
The Result
There were a few challenges that our distributor faced head on during this project due to the particular layout of the existing facility. Due to it’s L-shaped design, our distributor needed the new cleanroom to fit within a designated space, while meeting height restrictions and connecting it to the existing 2-story building. Our distributor accomplished this by coordinating the installation of a mezzanine to integrate the two buildings together while accommodating the extra space between them.
The completed installation resulted in a two-story building that housed laboratory space on the first floor and new office space on the 2nd floor. The cleanroom on the first floor was designed to meet ISO 6 (Class 1,000) classification and included a gowning room and pass through chambers to enhance operational efficiency.
Due to the cleanliness and speed of modular construction, our client was able to continue their manufacturing processes uninterrupted within the existing cleanroom while our distributor coordinated and completed the installation of the new cleanroom outside. The final building was completed within one month of signoff, falling inside of the client’s requested time frame.
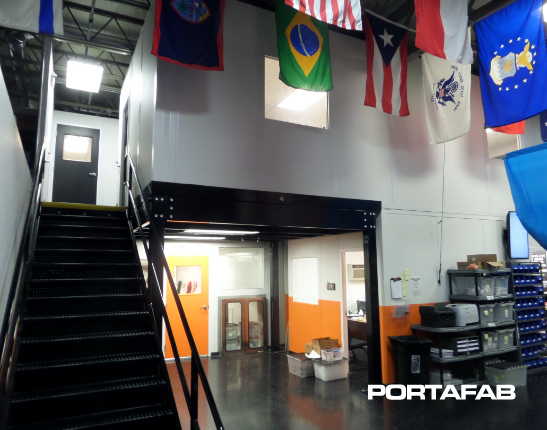